„Wenn die Norm erfüllt ist und ich dennoch Leute lange am Handy spielen oder Rauchen gehen sehe, muss wieder Luft im System sein. Ich komme da aber ohne die Mitarbeiter nicht ran.“ (Beobachtung der Produktionsleitung)
Das Erfahrungskurvenkonzept besagt, dass mit jeder Verdoppelung der kumulierten Ausbringungsmenge ein Einsparpotenzial von 20-30% bezogen auf die Stückkosten resultiert. Diese Potenziale können zu großen Teilen aber nur erschlossen werden, wenn die Ausführenden ihr Wissen und ihre Ideen einbringen.
Die MitarbeiterInnen einer Arbeitsgruppe wissen untereinander am besten um die Stärken und Schwächen der einzelnen Gruppenmitglieder und sie wissen auch um tagesformbedingte Schwankungen einzelner KollegInnen. Innerhalb gegebener Restriktionen kann die Gruppe daher selbst steuern, ob an einem Tag oder einer Schicht die vom Arbeitgeber gesetzte Norm erreicht wird.
MitarbeiterInnnen lernen, sich das Leben leichter zu machen. Sie haben aber selten einen Anreiz, solche durch Lernkurveneffekte und durch komplementäre Spezialisierung innerhalb einer Arbeitsgruppe resultierende Effizienzgewinne dem Arbeitgeber zur Verfügung zu stellen, insbesondere dann, wenn Vorgesetzte jede Art von Prozessoptimierung für sich reklamieren.
Die Übertragung der Erschließung von Optimierungspotenzialen an die Ausführenden trägt dazu bei, mit der vorhandenen Personalkapazität bessere Ergebnisse zu erreichen.
Anwendungsvoraussetzungen
- Mehrstufiger Produktionsprozess mit Liegezeiten, Rüstzeiten und Transportzeiten.
- Engpassfaktor ist die Personalkapazität, es liegen keine weiteren Engpässe, z. B. bei Maschinen, vor.
- Arbeitsorganisation in Arbeitsgruppen mit Mehrfachqualifikation der ausführend tätigen MitarbeiterInnen.
- Topmanagement gibt die Verantwortung an die Ausführenden und schließt explizit VorarbeiterInnen und MeisterInnen aus.
- Normen bezüglich des zu erzielenden Outputs sowohl für die einzelnen Maschinen, auf individueller Ebene als auch auf Gruppenebene.
- Anreizmechanismus zur Optimierung des Outputs auf Gruppenebene.
Wesentliche Schritte
Vorbereitung
- Identifikation von Fertigungsstrecken, in denen die notwendigen Vorrausetzungen vorliegen und die Produktionsleitung nicht erschlossene Potenziale vermutet.
- Überprüfung vorhandener Arbeitsanweisungen und Prozessbeschreibungen auf Aktualität (Beobachtung).
- Bobachtung und Gespräche mit den Mitarbeitenden, um die Vermutung von Optimierungspotenzial zu prüfen.
- Überprüfung möglicher Varianten im Entlohnungssystem, um die MitarbeiterInnen an den Einsparungen beteiligen zu können.
Durchführung
- Einladung zu einem Treffen mit den Mitarbeitenden, in dem die Notwendigkeit der Optimierung erläutert wird. Darüber hinaus sollte verdeutlicht werden, dass die Mitarbeitenden an Einsparungen beteiligt werden. Dabei auch Kommunikation der Kennzahlen, an denen die bessere Nutzung des Engpassfaktors Personal festgemacht wird, z. B. Maschinenstillstandszeit.
- Die Mitarbeitenden werden in Ihrer Arbeitszeit freigestellt, um gemeinsam Optimierungen zu überlegen. Hierzu kann auch ein evtl. vorhandener Innovationsraum genutzt und Kreativitätstechniken (wie z. B. die Methode 6-3-5) eingesetzt werden. Manche Mitarbeiterrunden fragen auch nach Begleitung durch z. B. eine vertraute MitarbeiterIn aus dem Qualitätswesen oder der Arbeitssicherheit.
- Test der erarbeiteten Vorschläge an einem oder mehreren Tagen/Schichten.
Auswertung und Nachbereitung
- Überprüfung der Maßnahme auf Wirksamkeit. Die Optimierung sollte nicht auf kurzzeitig erhöhte Anstrengungen zurückzuführen sein und eine sachlogische Erklärung haben.
Beispiel eines Ergebnisses: Abstimmung der individuell gesetzlich vorgeschriebenen Pausenzeiten in der Art, dass keine Maschine aufgrund von Pause des Personals heruntergefahren werden muss. - Überarbeitung von Arbeitsanweisungen und Prozessbeschreibungen.
- Einpflegen notwendiger Änderungen im Entlohnungssystem.
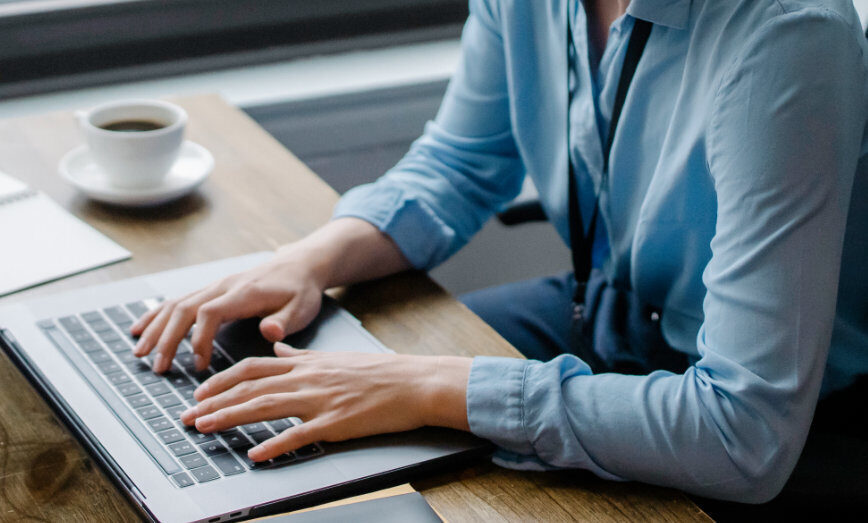
Sie haben Fragen zur Methode oder möchten gern weitere Informationen? Melden Sie sich gerne bei Dr. Matthias Orth von der SEALABLE Solutions GmbH!
Kennzahlen zur Erfolgsmessung
- Maschinenstillstandzeit.
- Durchlaufzeiten.
- First Pass Yield.
- Materialverbrauch.
- Stückkosten.
- Krankenstand.
Begünstigende Faktoren
- MitarbeiterInnen mit umfassender Erfahrung im zu optimierenden Arbeitsprozess.
- Hohe Bereitschaft der Gruppenmitglieder, sich wechselseitig zu helfen und zu unterstützen.
- Wechselseitige Wertschätzung der Stärken unter den Mitgliedern der Arbeitsgruppe/Schicht.
- Externer Anlass, über den die Notwendigkeit der Optimierung begründet werden kann, z.B. Kunde droht mit Kündigung des Auftrags.
Mögliche Herausforderungen
- MeisterIn und VorarbeiterIn sehen ihre Position gefährdet.
- Strohfeuereffekt, da erst mittelfristig erkennbare Konsequenzen nicht bedacht wurden.
- Veränderungen der Gruppenzusammensetzung, z. B. durch Krankheit oder neu eingestellte MitarbeiterInnen, gefährden die Funktion des Systems.
- Basieren die Effizienzsteigerungen auf einer komplementären Spezialisierung von zwei oder drei Mitarbeitenden, so müssen diese Mitarbeitenden auch gemeinsam in einer Gruppe arbeiten.
Weiterführende Links & Informationen
Presse & Medien
- Erfahrungsbericht: "Selbstorganisation in der Fertigung? Vier Erkenntnisse zur „Arbeit 4.0“ aus dem Gasturbinenwerk Berlin"
- Erfahrungsbericht: "Digitalisierung wird die Fabrikarbeit revolutionieren - Interview mit Hermann Arnold, Chairman von Haufe-umantis"
- Erfahrungsbericht: "In der Produktion in selbstverantwortlichen Teams arbeiten – geht das?"